離れた現場からも「今ある部品の数」が見える!棚卸差異を減らし、ミスが起きても原因を追える仕組みを構築
-
会社・団体名
-
株式会社ケイエムシステム
-
業種
-
小売・卸 / サービス
-
従業員数
-
~50名
-
地域
-
関東
-
管理物品
-
部品 / 部材
-
課題
-
紙やExcelでの管理をなくしたい
-
活用機能
-
入庫/出庫(予定)データ登録 / 項目追加 / データ一括登録/ダウンロード
2024/11/13
株式会社ケイエムシステム様:在庫管理基本情報
- 管理している物品:エスプレッソマシンの部品
- 管理している品目数:795品目
- zaico導入前の在庫管理方法:Excel
- 利用開始:2022年
- 利用頻度:毎日
- 利用人数:6~7名
- バーコード・QRコード利用:あり
zaicoを導入してよかったこと
- リアルタイムな在庫状況が離れた場所からもすぐにわかる
- 現場でお客様に正確なアナウンスができる
- ミスが起きたときに変更履歴や出庫一覧で原因を追える
株式会社ケイエムシステム様に、zaico導入のきっかけや導入後の効果について伺いました!
神奈川県横浜市に本社を構える株式会社ケイエムシステム様は、業務用エスプレッソマシンを中心とした設備機器の工事・修理・点検・保守業務を担う企業です。修理に使う部品の管理にzaicoをご利用くださっており、試行錯誤を重ねながら、よりミスの少ない運用を構築されています。
今回は、zaicoを使った業務改善に取り組まれているご担当の新井(あらい)様に詳しくお話を伺いました!
エスプレッソマシンの修理部品をzaicoで管理
――御社の事業内容と、管理されている物品をお伺いできますか?
新井様:弊社は主にエスプレッソマシンの整備・修理を行っており、それに使う部品や部材をzaicoで管理しています。消耗品も含め、金属部品など、マシンで必要とされるパーツはすべてzaicoに登録しています。
――修理の現場はどのあたりまで行かれるのですか?
新井様:本社は横浜市ですが、遠方だと長野県や群馬県へ出向くこともあります。
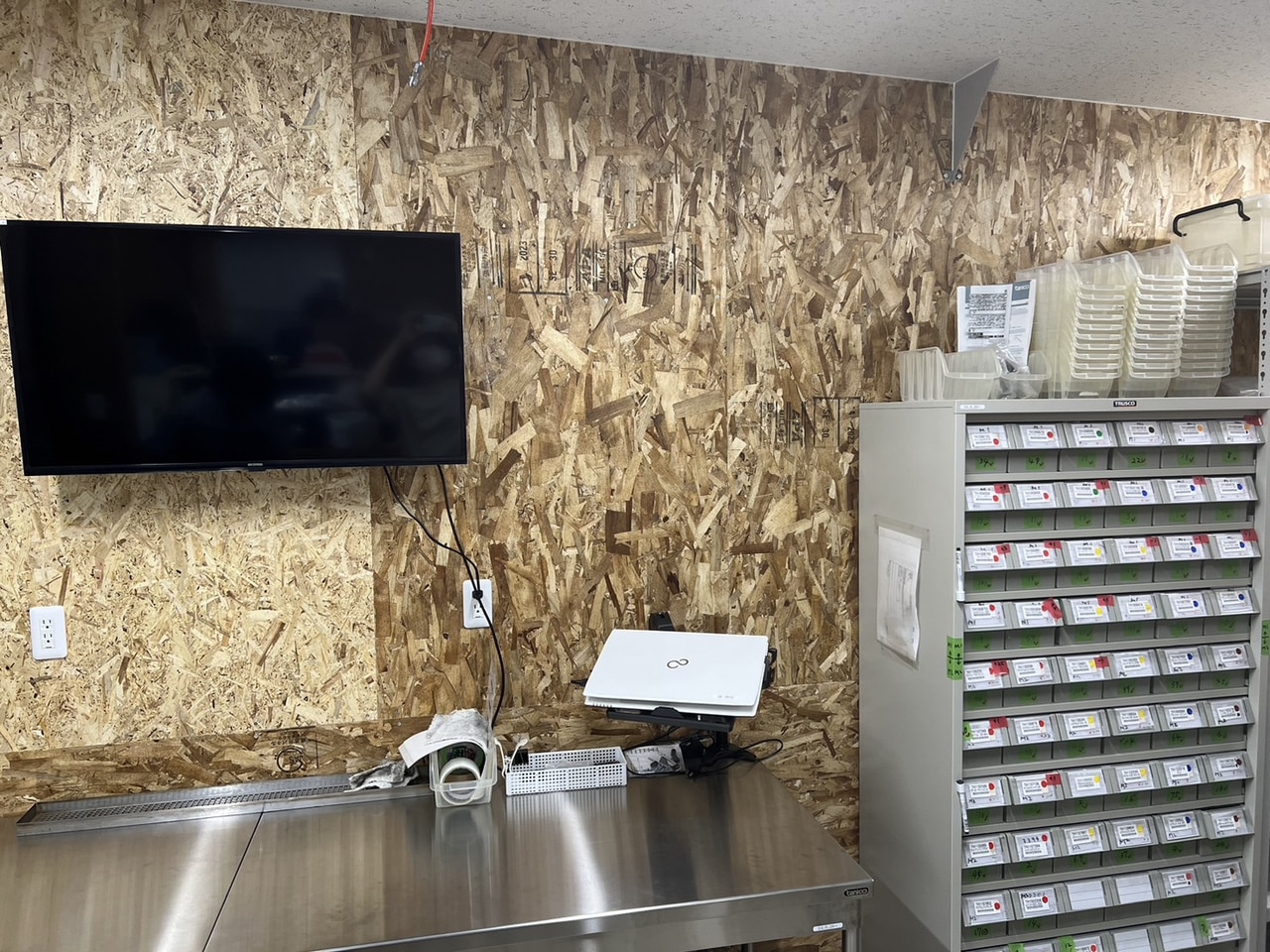
ケイエムシステム様オフィス
――zaico導入前はどのような在庫管理をされていましたか?
新井様:zaico導入前はExcelで在庫管理をしていました。部品番号と品数が現状どのくらいあるのかというのを、要所要所でカウントして把握するような形でした。
――入庫や出庫はどんな運用だったのでしょうか?
新井様:部品が入荷したら、Excelに入力して入庫処理をします。部品を使ったときは、リアルタイムに数を減らすといった運用はしておらず、使用した分まとめて後から数を差し引いたり、適宜残数を数えたりして把握していました。
当時はエスプレッソマシンの事業が始まったばかりというのもあって、物品の数もかなり少なかったので、いろいろと手探りで管理方法を模索しているところでした。
――エスプレッソマシンの事業を始めたのはいつ頃ですか?
新井様:2022年頃です。当初は、必要部品を取り寄せる供給元会社と一緒に在庫管理をしていたので、情報共有しながらはっきり業務の区別を付けずに運用している状態でした。
その後、本格的に稼働するようになり、案件数も爆発的に増えてきたので、弊社で在庫管理アプリを探しました。その中でzaicoがいいのではないかということになり、導入に至りました。zaicoの導入を決めたのは弊社代表です。
ミスを減らすため、zaicoを操作するスタッフを限定
――zaico導入時、現場でつまづきやネックはありませんでしたか?
新井様:むしろそれまでのやり方に限界があったので、どちらかというと早く何らかのシステムが欲しい状況だったこともあり、zaico導入に関してネックはありませんでした。
――zaicoは主にどなたが使ってくださっているのですか?
新井様:弊社のエスプレッソマシンに携わる部署の中でも、工場に属するスタッフと、マシンが設置されている店舗様に伺うスタッフがzaicoを使用しています。工場では、工場に保管されているものを管理。現場で修理を行うスタッフは、必要な部品をかいつまんで車載する(社用車に積む)のですが、その車載部品をzaicoで管理しています。
――工場スタッフ様と現場スタッフ様がそれぞれユーザー登録をされているのですね。
新井様:はい。工場スタッフで1ユーザーと、現場スタッフは車載する車ごとにユーザー登録をして、全部で6ユーザーほどで管理をしています。工場の人数は多いのですが、物品管理におけるミスを減らすために、部品そのものとzaicoに直接触れる人数を限定しました。そうすることで、管理の精度を上げられるという考えのもとでやっています。
――限られた方だけが触れるようになっているんですね。
新井様:はい。現場での部品管理としては、人ではなく車に紐づく形で運用しています。乗った車のアカウントを使って入出庫処理をするというオペレーションです。
入庫・出庫の登録にはバーコードスキャンを活用
――実際に修理をして部品が出庫する流れを教えていただけますか?
新井様:車載すべき基本部品がある程度分かっているので、あらかじめ必要数、車の在庫としてzaicoに登録しておきます。そして店舗様のところへ伺って、実際の症状を見て修理に取り掛かります。修理に使った部品を伝票に記入し、スマホのzaicoアプリからも使用した部品の出庫登録をします。
――出庫登録はバーコードを読み取って行っていますか?
新井様:はい。出庫はスマホで、各部品についているバーコードをスキャンして登録することが多いです。細かすぎて一個一個にバーコードが付いていない部品もあり、そういったものは手打ちで入力しています。
――なるほど。では、入庫はどのような処理をしているのですか?
新井様:供給元から弊社に入ってきた部品は、まず工場に入庫されます。バーコードをスキャンして数を入力し、zaicoに入庫登録をします。新しい部品があったら、新規在庫として追加登録をして数を入力します。
工場での在庫数が、基本的に会社全体の在庫のベースになっているので、修理のときはそこから必要数をzaico上の「車載」の棚に移動する、という形で運用しています。
zaicoを使うと現場で的確なアナウンスができる
――zaicoを導入した効果はありましたか?
新井様:新規事業を始めた初期の頃からzaicoを導入していたので、導入前後での変化というのはそれほどないんですが、在庫があるのかないのかという確認が現場ですぐにできるのは便利ですね。
――リアルタイムな在庫状況が分かるということですね。
新井様:はい。例えば現場で必要な部品がない場合、会社には在庫があるのか、それとも発注が必要なのかといった状況が明確に分かるので、その場でお客様に対してのアナウンスが的確にできます。それはzaicoを導入した良いところだと感じています。
棚卸ではzaicoの棚卸機能をあえて使わず「差異」を残す
――棚卸はどのようにされていますか?
新井様:zaicoとは別のシステムを使って棚卸をしています。システムといっても出納ができるものではなく、在庫数を数えるだけのシンプルなものですが。
――zaicoの棚卸機能は使用されていないのですね。
新井様:使っていません。理論在庫と実在庫でどれだけ差異が出ているのかを確認したいのですが、zaicoの棚卸機能を使うと、zaico上の在庫数を正しい数に上書きすることになるので、あえて別のシステムを使って棚卸をしています。
――zaico上の在庫数と、実在庫数の差を残しておく必要があったのですね。
新井様:はい。実は供給元の棚と弊社の棚を合わせる作業を積極的にやっていたのですが、数がズレている状態が続いていました。その差異がどれだけ発生していたかを確認したかったんです。供給元に対しても差異を見せるという意味で、zaicoと実棚の差をそのまま残して使っています。
棚卸差異は減ってきた。今後はミスが起きやすい「穴」を潰していきたい
――ズレが生じる原因は何だったのでしょうか?
新井様:ヒューマンエラーが多くて。やはり細かい部品の取り扱いでミスが起きたり、使おうとしたけれど使わずに戻したり、動きの中で追えないものが多々ありました。結果、実棚との差異が出てしまっているので、その動きを見たかったんです。
――今後はどのように棚卸を行われる予定ですか?
新井様:前回の棚卸でいったん一区切りついたので、これからどうするかを考えていくことになります。今後は年に3〜4回棚卸をしていくことになりそうですが、棚卸自体をどういう形で進めていくか検討が必要です。
――供給元様と情報共有しながら棚卸をしていくのですね。
新井様:はい。これまでは供給元と別々で棚卸をしていて、数も合っていませんでした。zaicoはあくまで自己管理のために弊社で使っていたのですが、物品数もどんどん増えて、供給元とも在庫情報の共有をどうするかという話し合いが持たれました。ここ一年はzaicoを使った管理・運用についてお互いに確認し、明確化していったという経緯です。
棚卸に使っている別システムは単純に数を数えるだけのものなので、今後もzaicoと併用していくのが供給元との整合性も取りやすいと今のところは考えています。
――今の運用を、今後どのようにより良くしていこうかという段階なのですね。
新井様:そうですね。今は我々の運用方法を「こういうときはこうします」と明確にしていっているところです。それで先ほど言ったように、zaicoにアクセスできる人を限定したりしています。関わる人が増えるほど、その分処理し忘れや、数を間違えるリスクも上がりますので。
――運用を固めていく中で、ミスは減りましたか?
新井様:そうですね、棚卸差異はかなり減りました。去年の秋ごろから管理権限を持っている者を限定し、かつ物品を動かしたときの記録をしっかりと取っておき、それをzaicoに反映させるという運用で在庫管理の精度を上げているところです。
――より精度が高まっているということですね!理想はやはり「差異0」でしょうか?
新井様:そこ(差異0)を目指してはいますが、人が関わる限り不可能というのは分かっているので、ミスが起きたときに追えることが重要と考えています。
zaicoのデータと「整備表」でミスをチェック
――ミスはどのようにして追う仕組みを作られているのですか?
新井様:今はzaicoの変更履歴や出庫リストと、工場にある「整備表」という手書きのシートを使ってミスを調査しています。
――「整備表」はどのような使い方をするのでしょうか?
新井様:工場のスタッフが整備表に必要部品を書いてzaicoの担当者に渡し、zaico担当者が部品を棚から持ってきて現場のスタッフに渡します。現場スタッフが部品を使って整備を終えたら、zaico担当者に使ったもののリストを提出します。そこで、使用した部品と整備表を照らし合わせて、バーコードスキャンをして出庫登録をしています。
新井様:出庫登録のときは、数を入れた後に出る確認画面をスクリーンショットに撮って、整備表と一緒に保存しています。
新井様:この運用で、ミスがあったときに気づきやすくなる環境を作っています。また、スクリーンショットと出庫履歴を照らし合わせたときに、数がズレていたら逐一修正しています。
――徹底されていますね!
新井様:正直、これでも穴はあります。ただ、どこでミスが起きやすいかが分かってきたので、そこを意識すれば可能な限りミスを減らせるというところまでは来ています。いかにその穴を潰していけるかが今後の課題です。
――本日は貴重なお話をお聞かせくださり、ありがとうございました!
設備機器の部品管理にzaico
今回は、エスプレッソマシンを主とした設備機器の部品管理にzaicoを活用されている、株式会社ケイエムシステム様の導入事例をご紹介しました。ご担当の新井様が「人が介入する限りミスを0にするのは難しいが、ミスの原因を追って一つずつ潰していくことが大事」と仰り、運用フローの改善を重ねている姿が印象的でした。
ケイエムシステム様と同様の業種の方で、部品の在庫管理にお悩みの方はぜひ今回の事例を参考にしてみてください!